ID Technology’s Model 255 Label Printer Applicator is designed to PackML standards and provides enhanced communications, using an Allen-Bradley PLC and a color touchscreen interface.
PackML provides equipment manufacturers with a structured controls programming philosophy and customers with a standardized look and feel of the machine HMI (Human Machine Interface). This reduces operator training since the controls of each packaging machine are immediately familiar, with common error reporting and screen layouts.
In addition by standardizing machine mode, states and tags, PackML allows for communication between systems, both within the modules of a machine and other machines on a packaging line - regardless of the brand of controls that is used.
The Model 255 is controlled by an Allen-Bradley Micro850® Programmable Logic Controller in conjunction with a 4.3 inch touchscreen interface. The various screens on the touchscreen display are programmed to be compatible with PackML standards. If your company has adopted PackML for packaging equipment, the 255 is the best way to ensure you get the PackML benefits throughout your entire packaging operation.
Don’t use PackML, but want Allen-Bradley integrated controls? The Model 255 is a great option for you as well. With its Micro850 controller, Ethernet/IP & Modbus communications the 255 is ready for your integration team to build into your packaging operation. Having the machine HMI designed to solid PackML principles ensures that your operators and technicians will be comfortable with interacting with the equipment.
Like all ID Technology print and apply labeling systems, the Model 255 is designed on the Centerline-Modularity™ principle. This simplifies the set-up, operation and support of the equipment by eliminating as many adjustment points as possible. The result is increased uptime and lower operating costs for the customer.
The Model 255 can be equipped with any of ID Technology’s wide selection of label application modules, making it capable of handling just about every conceivable labeling job.
The Model 255 can be used to label cases, pallets or most other items and can apply up to three labels per package, depending on your application.
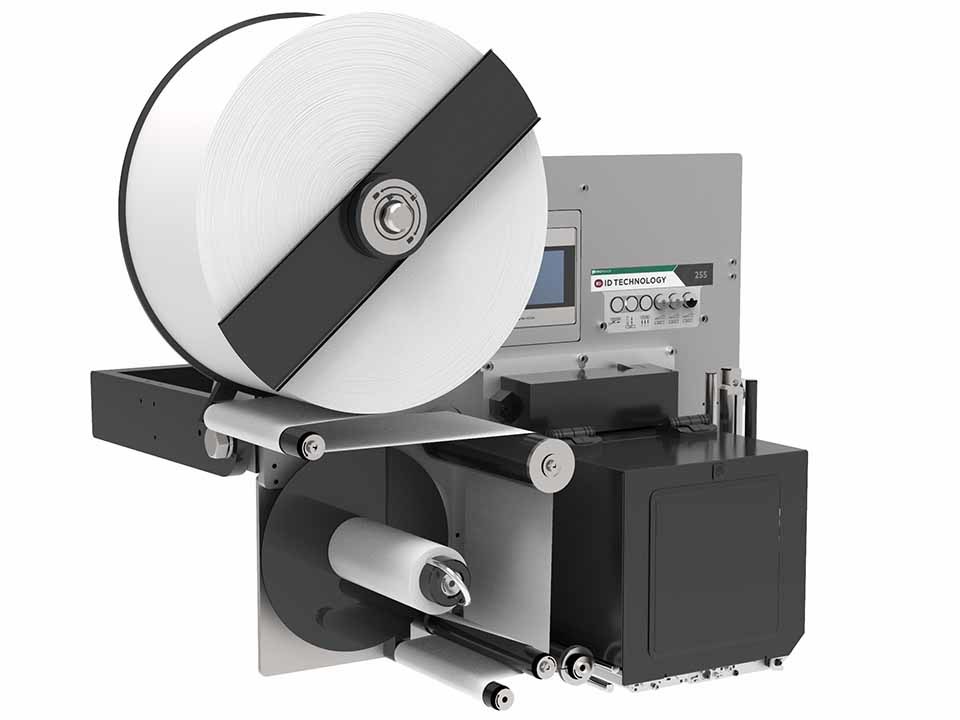
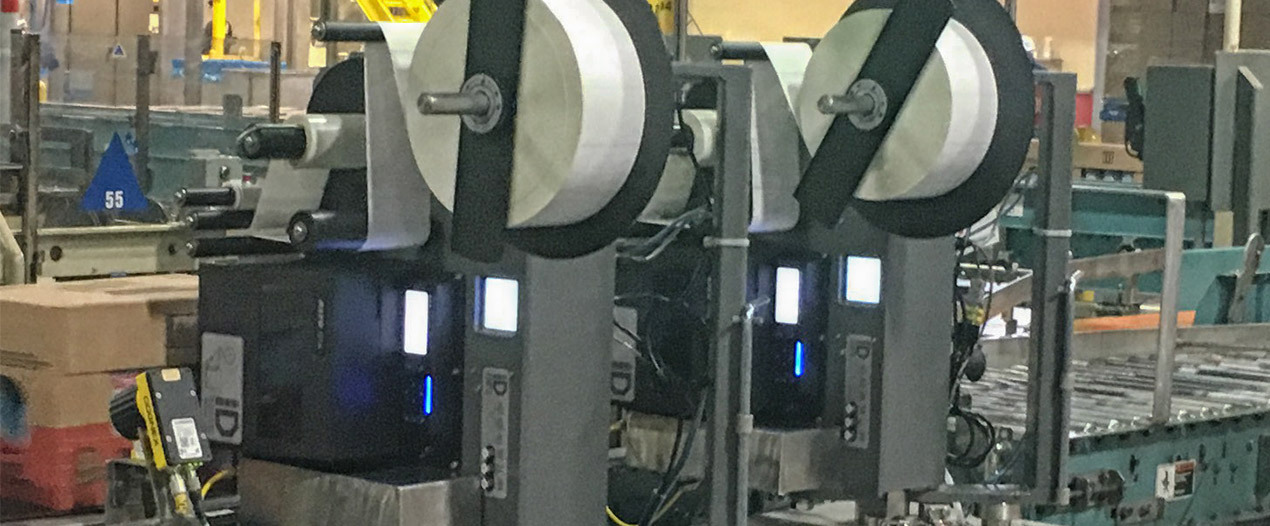
Product Overview
Easy Line Integration
Control Remotely
- The 255 is built on the Allen-Bradley control platform allowing for easy integration into line control systems with Ethernet/IP and RS232/RS485 built-in.
- This labeling system can also be supplied with an Allen-Bradley Flex I/O unit as an alternative to the PLC. This allows the complete system to be controlled remotely from a customer-supplied Allen-Bradley PLC.
Configurable
Applicator Options
- As part of ID Technology’s 252 family, the 255 can be configured with any of the wide array of applicator modules and mounting hardware options that are available - the 255 can handle just about every labeling job.
PackML
Maximize the Value of Packaging Machinery
- PackML provides equipment manufacturers with structured controls.
- PackML reduces operator training since the controls of each packaging machine are immediately familiar, with common error reporting and screen layouts.
- PackML allows for communication between systems, both within the modules of a machine and other machines on a packaging line - regardless of the brand of controls that are used.
Solutions for:
Senior Leadership
Your Challenges:
- Your business is moving forward with Industry 4.0 and connected systems.
- Your company has made a large investment in adapting PackML as a standard for packaging line control.
Our Solutions:
- The ID Technology 255 print and apply labeling system is designed with enhanced communications, allowing it to easily communicate with other equipment and with your manufacturing software.
- The controls of the 255 are designed to be compliant with the PackML standard, allowing easy integration with PackML controlled packaging lines and equipment.
Operations Management
Your Challenges:
- Your company has chosen to standardize on a particular control system for all packaging equipment.
- Having a mix of different manufacturers' packaging machines makes it complicated for spare parts, repairs, and operators.
- Changing labeling demands from customers can quickly make equipment obsolete.
Our Solutions:
- The 255 is built to use Allen-Bradley PLC controls - the most often specified systems. In addition, the robust PackML compliance combined with extensive communications ability enables the 255 to be used in many different control and data environments.
- ID Technology's 255 system is built on the proven 252 platform. Other than the controls, all the machine modules are the same - for existing customers, this means the same parts, and also much the same procedures to operate.
- The modular design of the 255 and the access to the wide portfolio of ID Technology applicator modules, mean that the 255 can be quickly reconfigured in the event of changes to labeling applications.
Operators & Technicians
Your Challenges:
- Adding new model equipment to packaging lines can cause problems with having to keep additional spare parts as well as needing to learn how to maintain new systems.
- There is always pressure to reduce downtime on the packaging lines.
- The training your maintenance and operator team receives isn't always helpful.
Our Solutions:
- ID Technology's 255 is designed around the market-leading 252 labeling system. Other than the controls, all of the modules that make up the system are the same and interchangeable with your existing ID Technology equipment.
- In many cases, your company can purchase pairs of 255 labelers to work in zero-downtime mode. This can eliminate the need to stop production to replenish labels and ribbons. Less downtime = happy management!
- ID Technology field service technicians are graduates of the PMMI Certified Trainer program. You can be assured you will get the best professional training for more maintenance folks and line operators.
Contact an ID Technology Account Manager
Ready to improve your production output and operational efficiency? Contact an ID Technology account manager today to learn how our labeling and coding automation solutions will increase your throughput and improve your bottom line.