Combining speed, safety, and simplicity, the Model 258 barcode label applicator is a superior solution for high-speed case and tray labeling. Engineered to outperform competing systems, it eliminates compromises with innovative features and seamless integration into production lines.
Using patented CrossMerge® technology, the Model 258 decouples print speed from applicator speed, enabling slower, higher-quality printing while applying labels up to 50% faster than the competition. This advanced design ensures superior throughput without sacrificing precision.
The Model 258 also offers features that set it apart from other barcode label applicators:
- Labels are printed along the narrower dimension, allowing for more labels per roll and reducing replenishment time.
- Barcodes are printed and applied in the preferred orientation, eliminating the need to slow down or stop for label application.
- Expanded reach: the Model 258 can reach up to 6 inches across conveyor lines.
- It’s all-electric, reducing operational expenses by eliminating the need for compressed air.
Built to meet the rigorous demands of material handling and supply chain operations, the Model 258 bar code label applicator delivers unmatched efficiency and reliability for automated case and tray labeling.
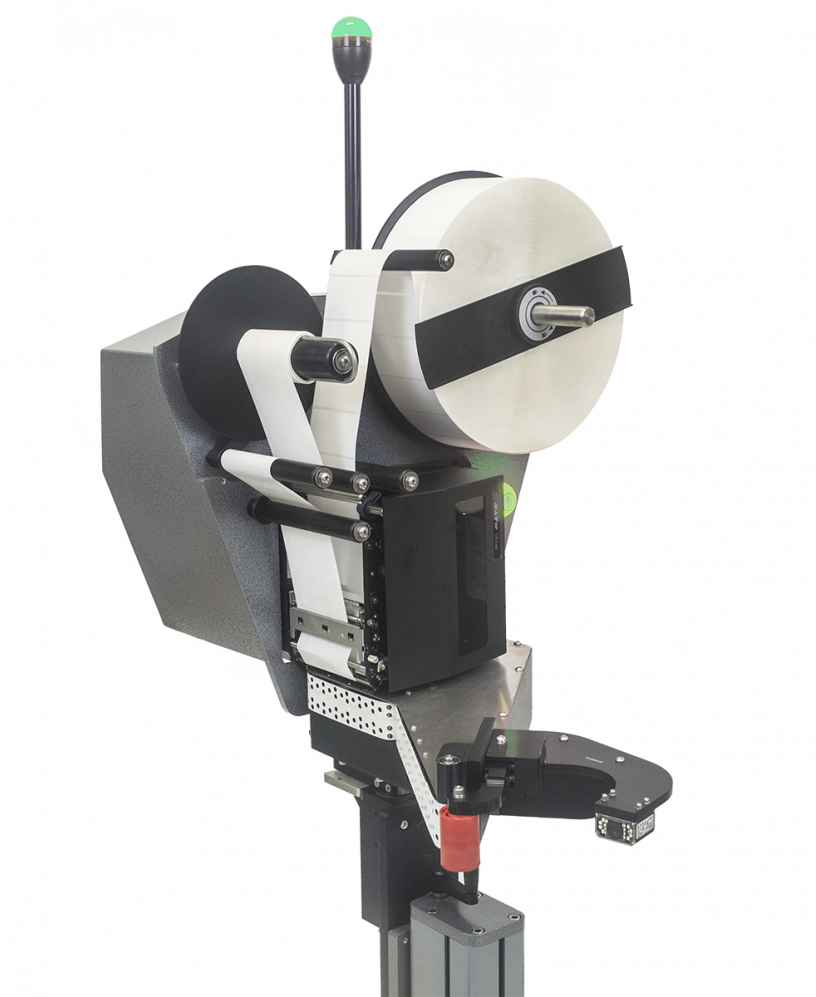
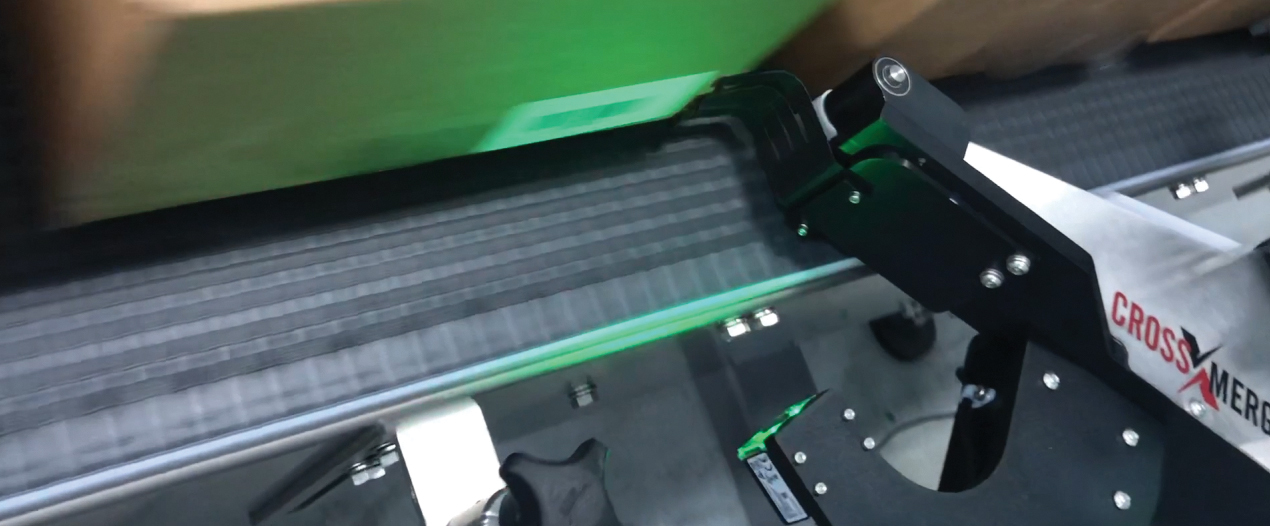
Product Overview
Engineered for Speed
Leveraging patented CrossMerge® technology, the Model 258 barcode label applicator decouples print speed from application speed. This ensures slower, high-quality label printing while enabling faster label application for optimized throughput. The result is exceptional label and barcode quality, regardless of production speed demands.
- The 258 prints labels/barcodes at an optimum speed for increased quality and readability. Better scans translate to fewer rejections down the line.
- The applicator speed, separate from the print speed, is 50% faster than competitor systems and matches conveyor rates of 200 ft/min or more to achieve greater throughput of your items.
- To really boost your throughput, integrate two 258 systems in tandem and achieve zero downtime in your operations.
Engineered for Safety
The Model 258 barcode label applicator prioritizes operator safety with features that enable secure interaction during service, maintenance, or label roll changes—even during live operations. Designed for high-speed labeling, it ensures optimal performance without compromising safety, delivering reliability and peace of mind for operators.
- The 258 swings away from the conveyor – and automatically switches offline when rotated – to provide safe, unobstructed access for operators.
- No pinch points from reciprocating parts.
- Applicator belt automatically disables when system is set to offline or rotated away from the conveyor.
- For added safety during operator service or maintenance, the applicator arm swings away for even easier access.
Engineered for Simplicity
The Model 258 barcode label applicator is thoughtfully designed for operator ease, combining simplicity and high performance. This automated case and tray labeling system ensures efficient, user-friendly operation while delivering top-tier results in high-speed labeling applications.
- We’ve eliminated the traditional HMI in favor of a singular color-coded button that performs all of the functions you need to operate the 258 with a simple push. That means no menus or pages to navigate within a display.
- The 258 prints labels along the narrow dimension, equating to having twice as many labels available per roll and reducing the number of label changeovers.
- Barcodes are printed and applied in the preferred orientation, meaning there is no need to slow your rate (or stop completely) to apply labels.
- The 258 is comprised of modular components for easy and efficient service and maintenance, when required.
- Optional integrated scanner provides pre-programmed barcode verification immediately after label application for even greater simplicity.
Solutions for:
Senior Leadership
Your Challenges:
- Increased throughput in your operations.
- Reduce unnecessary expenses from chargebacks due to poor barcode quality.
Our Solutions:
- Up to 50% faster than competitor systems.
- Application speed matches line rate (up to 200 ft/min or more), so you label more product.
- Utilization of two 258s in tandem provide a Zero Downtime solution.
- Barcodes printed at ideal quality due to printing in the short direction. Optional camera verifies barcode readability immediately after label application.
Operations Management
Your Challenges:
- Downtime due to increased operator interaction with labeling systems.
- Reduction of utility costs.
- Replacement of inkjet solutions that yield poor quality barcodes, or inability to imprint on shrink-wrapped trays.
- Minimal floor space available for labeling system / reach to product.
Our Solutions:
- Since labels are printed in the short direction, the system yields more labels per roll and requires fewer changeovers by operators = less downtime.
- System is all-electric, so no compressed air is needed, reducing your overall operating costs.
- Thermal Transfer or Direct Thermal label imprint options provide better quality barcodes (and inkjet not applicable for shrink-wrapped trays).
- Compact footprint, with ability to reach up to 6" across conveyor.
Operators & Technicians
Your Challenges:
- The number of label changeovers that occur during a shift, leading to increased downtime.
- Complex maintenance or service of the label applicator.
- On-the-job injuries due to system complexity or interaction with system in close proximity to conveyor lines.
- Complex system interface.
- Preventative maintenance notifications not allowing proactive maintenance.
Our Solutions:
- Less need for label changeovers since more labels are available per roll = less downtime.
- System features modular components for ease in maintenance or parts replacement.
- No reciprocating parts or pinch points.
- Entire system swings away from live conveyor line for safer interaction.
- Singular, color-coded button replaces HMI. So no complex menus to navigate.
- Optional barcode camera alerts you when printhead service is needed.
Contact an ID Technology Account Manager
Ready to improve your production output and operational efficiency? Contact an ID Technology account manager today to learn how our labeling and coding automation solutions will increase your throughput and improve your bottom line.